Preventive vs. Predictive: Which Switchgear Maintenance Strategy Saves More Money?
by Nicholas Nashed on May 06, 2025
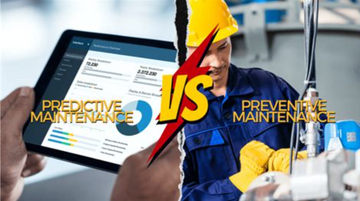
When it comes to maintaining low and medium voltage switchgear, facility managers often
debate between preventive maintenance and predictive maintenance strategies. Both
approaches aim to reduce equipment failure, improve uptime, and ensure electrical safety—but
which one delivers better value?
Understanding the differences between these strategies is critical for optimizing your electrical
infrastructure and minimizing unplanned downtime.
Preventive Maintenance: The Traditional Safety Net
Preventive maintenance relies on scheduled inspections and routine servicing, typically based
on manufacturer recommendations or time intervals.
Key Features of Preventive Maintenance:
Regularly scheduled tests and inspections
Replacement of aging components regardless of current performance
Follows NETA and ANSI standards
Useful for compliance and warranty retention
Reduces the risk of catastrophic failure from overlooked wear
Drawback: May lead to unnecessary service costs or part replacements that still have useful life left.
Predictive Maintenance: Smarter, Data-Driven Care
Predictive maintenance uses real-time data and advanced diagnostics to determine equipment
health and forecast potential issues before they happen.
Key Features of Predictive Maintenance:
Utilizes thermal imaging, breaker timing, and insulation resistance trends
Condition-based servicing (only when needed)
Enables better resource allocation and reduced operational disruption
Ideal for critical or high-load environments
Supports long-term cost reduction and equipment longevity
Drawback: Requires investment in monitoring tools and expertise to interpret results effectively.
The Smartest Approach: Combine Both
For mission-critical facilities, blending preventive and predictive strategies often yields the
best return on investment (ROI). Preventive routines serve as a baseline, while predictive
insights allow for smarter, more precise maintenance interventions.
How AK&J Electric Supports Your Facility:
Preventive maintenance scheduling and full NETA testing reports
Predictive diagnostics using advanced tools like thermal imaging and breaker analysis
Data interpretation and actionable insights
Support for compliance with OSHA, NFPA 70E, and insurance requirements
Reduction in unplanned downtime and long-term maintenance costs
For critical operations, we recommend a hybrid approach—leveraging preventive routines for
compliance and predictive tools for cost savings.
Protect your facility, equipment, and personnel with a smarter maintenance strategy.
Contact AK&J Electric today to learn how we can support your switchgear reliability goals.